Digitale Zwillinge sind mehr als nur ein Schlagwort für Industrieunternehmen. Virtuelle Modelle physischer Objekte können die Effizienz steigern und die Kosten in allen Phasen der Produktentwicklung und des Produktlebenszyklus senken. Digitale Zwillinge und Prototypen können die Art und Weise, wie Unternehmen arbeiten, verändern – vielleicht sogar ganze Branchen.
In diesem Artikel erzählen wir Dir
- Was digitale Zwillinge und digitale Prototypen sind und wie sie in Industrieunternehmen eingesetzt werden.
- Welche Vorteile Industrieunternehmen daraus ziehen können, dass sie die physische Welt mit der digitalen Welt verbinden.
- Wie Unternehmen mit Industrie 5.0 neue Geschäftsmöglichkeiten erschließen können.
Die Aufgabe ist einfach: Mit dem Traktor über den Hof fahren und einen Heuballen aufheben. Mit einer Drehung des Schlüssels springt der Motor an und der Traktor rollt zu den Ballen.
Der Testfahrer versucht, die Gabel zu bedienen, aber während er sich darauf konzentriert, die richtige Taste auf den Bedienelementen zu finden, dreht er versehentlich das Lenkrad. Der Traktor biegt nach links ab und fährt direkt in einen Graben. Dort bleibt er liegen, der Motor läuft weiter, die Gabel bleibt am Boden hängen und hebt das Cockpit hoch. Die Hühner auf dem Hof schwirren umher und bemerken den Unfall nicht.
Olli Kauppinen verfolgt die Eskapaden des unerfahrenen Testfahrers mit einem amüsierten Gesichtsausdruck. Wäre die Maschine echt gewesen, eine kommende neue Version des Valtra-Traktors im Wert von Hunderttausenden von Euro, hätte seine Reaktion ganz anders ausfallen können.
Der Bauernhof mit seinen Heuballen, Hühnern und gefährlichen Gräben existiert nur in der digitalen Welt.
Der Testfahrer sitzt in einem Traktorsitz mit echten Pedalen und Bedienelementen im AGCO-Büro in Jyväskylä, Mittelfinnland. Wir sind etwa 45 Kilometer von der Fabrik entfernt, in der der hochmoderne Traktor gebaut werden wird. Neben dem Sitz stehen drei riesige Server, auf einem von ihnen läuft die Simulation.
Der Software-Validierungsingenieur Olli Kauppinen und sein Team haben fast zwei Jahre lang an dem digitalen Prototyp des Traktors gearbeitet, wobei das Team von zwei auf fast zehn Personen angewachsen ist. Der digitale Prototyp ermöglicht es dem Team, die Software des Traktors ohne einen physischen Prototyp zu testen.
Der Bauernhof mit seinen Heuballen, Hühnern und gefährlichen Gräben existiert nur in der digitalen Welt.
Der Prototyp umfasst die meisten Funktionen der Maschine – von der Hydraulik und Pneumatik über den Motor und das Getriebe bis hin zur Steuerung. Er ahmt auch die vielen Möglichkeiten nach, wie der Traktor mit der Welt interagiert, z. B. wie sich die Form des Geländes auf die Systeme auswirkt oder das Gewicht der Ladung.
„Wir können die aktuelle Software testen und verschiedene Lösungen, wie z. B. neue Sensortypen, auf agile Weise ausprobieren. Außerdem ist es einfacher, verschiedene Fehler, wie z. B. eine Sensorfehlfunktion, in einer digitalen statt in einer physischen Umgebung zu simulieren. Das spart Zeit bei der Produktentwicklung“, erklärt Kauppinen, sichtlich stolz auf die Leistung seines Teams.
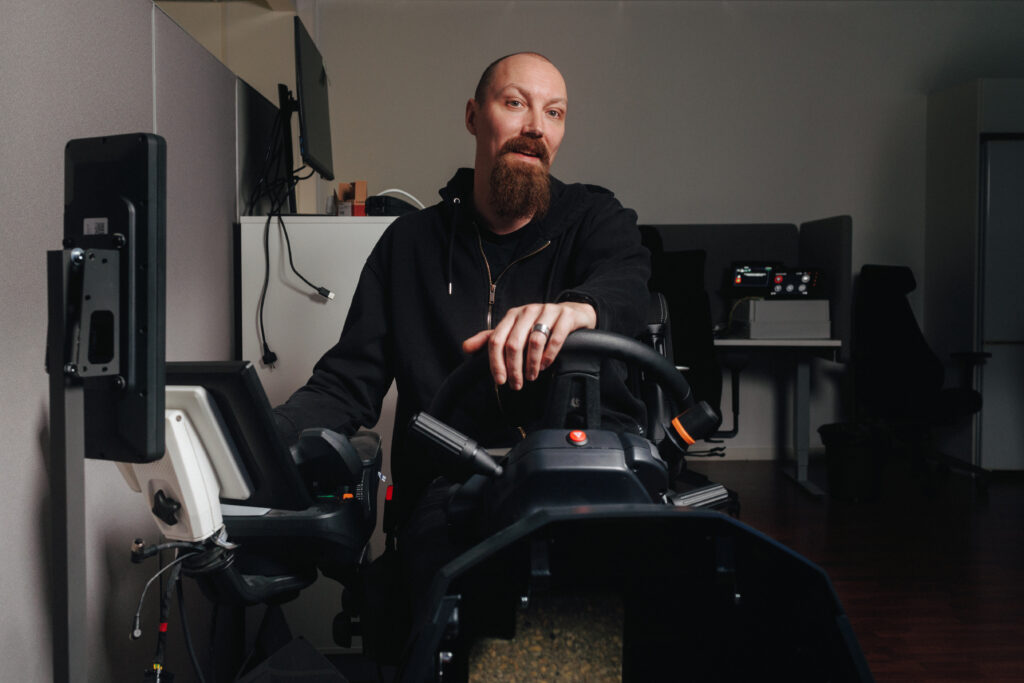
Willkommen in der Ära der digitalen Zwillinge
Digitale Zwillinge sind, kurz gesagt, virtuelle Modelle von physischen Objekten. Sie können ein einzelnes System, ein komplettes Produkt oder einen ganzen Prozess, wie ein Feld oder eine Fabrik, abbilden. Einige digitale Zwillinge haben eine visuelle Darstellung, wie die neue Version des Valtra-Traktors auf dem Bildschirm im AGCO-Büro, aber oft sind es nur Daten. Wenn es ein reales physisches Gegenstück des Produkts gibt, nennt man das virtuelle Modell einen digitalen Zwilling. Ein digitaler Prototyp kann dagegen auch nur eine virtuelle Version sein.
Besonders attraktiv ist das Konzept in der Fertigungsindustrie, wo der weltweite Markt für digitale Zwillinge laut dem deutschen Datenportal Statista bis Mitte der 2020er Jahre mehr als 6 Milliarden Dollar (5,5 Milliarden Euro) erreichen wird, mehr als zehnmal so viel wie zu Beginn des Jahrzehnts.
Der Reiz des digitalen Zwillings ist leicht zu verstehen: Die digitale Version eines komplexen physischen Objekts kann wertvolle Ressourcen in der Entwicklungs-, Produktions- und Testphase einsparen und ermöglicht es, mögliche mechanische oder kodierte Probleme zu erkennen, noch bevor eine physische Version des Geräts existiert.
Eine digitale Version eines komplexen physischen Objekts kann wertvolle Ressourcen in der Entwicklung, Produktion und beim Testen einsparen.
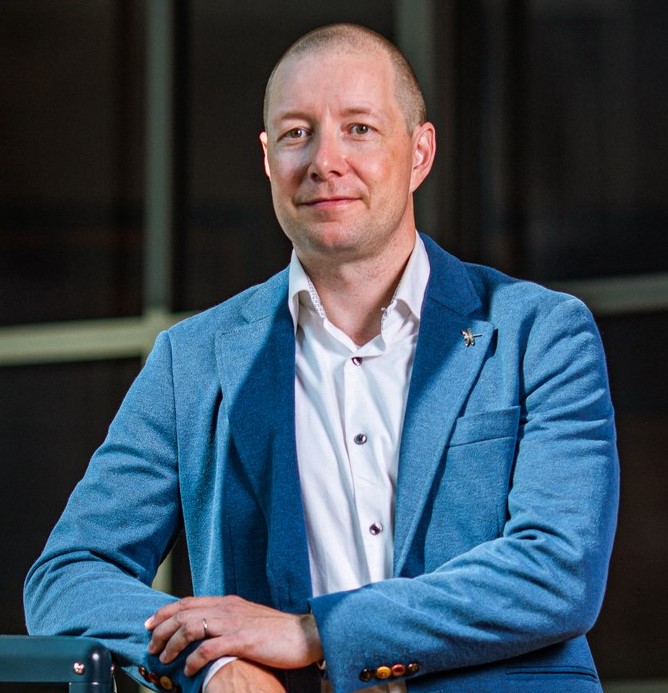
In der industriellen Produktentwicklung und -prüfung besteht einer der größten Vorteile des digitalen Prototyps oder digitalen Zwillings darin, dass er mehrere Disziplinen unter einem digitalen Dach vereint und so den Entwicklungsprozess verbessert und beschleunigt, sagt Harri Laukkanen, Direktor für industrielle Digitalisierung bei Gofore, einem langjährigen Partner von AGCO.
Er hat eine lange Erfahrung mit intelligenter Industrie- und Schwermaschinensoftware und hat aus erster Hand erfahren, welche Fallstricke organisatorische Silos mit sich bringen und wie langsam und starr die traditionelle Produktentwicklung sein kann.
„Wenn die Maschine früher nicht funktionierte, bedeutete das, dass ein Fehler in der Mechanik, im Hydraulikplan oder in der Codierung vorlag. Um herauszufinden, wo genau das Problem lag, brauchte man Zeit. Wenn wir dies in einer virtuellen Umgebung tun, können wir Dinge wie Hydraulik und Mechanik gemeinsam mit einem funktionsübergreifenden Team modellieren und testen. Auf diese Weise können wir Probleme sofort erkennen.“
Ein digitaler Zwilling kann auch in der Ausbildung eingesetzt werden. Das Erlernen der Bedienung anspruchsvoller Maschinen wird einfacher, intuitiver und sicherer – und relativ kostengünstig, da teure Maschinen nur in der virtuellen Realität im Graben landen. Der Zwilling ist auch wertvoll, wenn es darum geht, den Wartungsbedarf zu erkennen und die Produktion zu überblicken, sei es in der Fabrikhalle oder auf dem Feld.
Laukkanen glaubt, dass digitale Zwillinge zur Lösung vieler Probleme beitragen können, mit denen Industrieunternehmen heute konfrontiert sind, wie etwa steigende Kosten und der Druck, schnell (aber mit angemessener Qualität) auf den Markt zu kommen. Eines der größten Versprechen der digitalen Zwillinge besteht darin, Unternehmen dabei zu helfen, sich in einem zunehmend komplexen Umfeld zurechtzufinden, in dem Kunden und Gesetzgeber immer höhere Anforderungen an Benutzerfreundlichkeit, Energieeffizienz und Nachhaltigkeit stellen.
„Produkte, einschließlich schwerer Maschinen, werden zunehmend elektrisch und automatisiert, und wir werden mehr Hybridlösungen und autonome Maschinenflotten sehen, die ohne Menschen zusammenarbeiten.“
Digitale Zwillinge können Unternehmen helfen, sich in einem zunehmend komplexen Umfeld zurechtzufinden, in dem Kunden und Gesetzgeber immer höhere Anforderungen an Benutzerfreundlichkeit, Energieeffizienz und Nachhaltigkeit stellen.
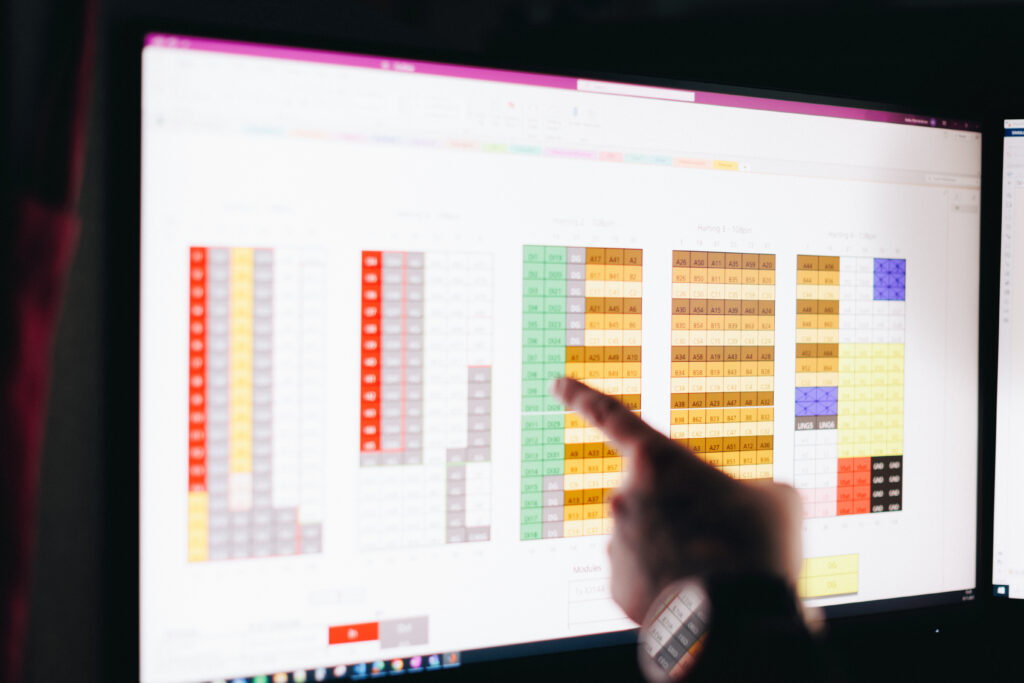
Mit dem digitalen Lebenszyklus neue Möglichkeiten erschließen
Digitale Zwillinge und damit verbundene Technologien wie künstliche Intelligenz, das Internet der Dinge, Cloud Computing und das Metaversum sind bereits mehr als nur Schlagworte in der industriellen Landschaft. Unternehmen auf der ganzen Welt investieren in großem Umfang in intelligente Produkte und Dienstleistungen, die die digitale und die physische Welt miteinander verbinden.
Einem Bericht von Capgemini zufolge werden 88 % der Unternehmen in den nächsten fünf Jahren intelligente Dienste anbieten, und fast die Hälfte erwartet, dass ein erheblicher Teil ihres Umsatzes aus intelligenten Diensten stammen wird.
Die Übertragung der physischen Welt auf die digitale Welt eröffnet den Unternehmen immense Möglichkeiten. Wenn digitale Zwillinge in die strategische Planung eingebettet werden, können Unternehmen ihre Produktivität und ihre Abläufe optimieren und gleichzeitig neue Arten von Erfahrungen bieten, sagt Dr. Zhihan Lyu, Professor an der Universität Uppsala, Schweden.
„Durch die Digitalisierung der gebauten Welt mittels digitaler Zwillinge können Unternehmen den Wert ihrer Vermögenswerte für jeden Ort der Welt erschließen, was zur Entstehung einer potenziell unbegrenzten Anzahl von Metaversen-Diensten führt.
Digitale Zwillinge sind die Bausteine des Metaversums, einer gemeinsamen und immersiven virtuellen Erfahrung. Im Metaverse könnten Unternehmen zum Beispiel Schulungen und Wartungsworkshops aus der Ferne abhalten oder ihre Produktionsanlagen besichtigen. Laut McKinsey könnte das „Unternehmens-Metaverse“ letztlich eine vollständig digitale Version der gesamten Lieferkette eines Unternehmens sein, von den Rohstoffen bis hin zu Vertrieb und Wartung.
Unternehmen müssen mehr tun, als der physischen Welt eine digitale Schicht hinzuzufügen, um das Beste aus digitalen Zwillingen oder anderen intelligenten Lösungen zu machen. Laukkanen von Gofore ermutigt Unternehmen, den gesamten digitalen Lebenszyklus eines neuen Produkts zu berücksichtigen und die Digitalisierung in das Geschäftsmodell zu integrieren.
„Unternehmen müssen mehr tun, als der physischen Welt eine digitale Ebene hinzuzufügen, um das Beste aus digitalen Zwillingen oder anderen intelligenten Lösungen zu machen.“
„Schon zu Beginn der Produktentwicklung können wir uns Gedanken über das Design machen und darüber, wie die Maschine genutzt werden soll oder wie wir die Anforderungen an Effizienz und Nachhaltigkeit erfüllen können. So können wir frühzeitig simulieren, ob es möglich ist, eine Maschine mit den Bausteinen zu bauen, die wir verwenden wollen.“
Da die Produkte immer komplexer werden und fast jede Maschine ein digitales, mit der Cloud verbundenes Herzstück hat, wird die Konfigurationssteuerung zentral. Schwere Maschinen, wie z. B. Traktoren, werden in der Regel auf die Spezifikationen des jeweiligen Kunden zugeschnitten. Digitale Prototypen können dabei helfen, alle Varianten zu testen, lange bevor die Maschinen gebaut werden.
Um den Punkt zu erreichen, an dem das Denken in digitalen Produktlebenszyklen ein integraler Bestandteil der täglichen Arbeit des Unternehmens ist, sind Zeit, strategische Planung und Veränderungsmanagement erforderlich, so Laukkanen. Als Partner für die industrielle Digitalisierung hilft Gofore Unternehmen bei der Transformation.
„Die Implementierung des digitalen Lebenszyklus in der Produktentwicklung und in den Prozessen kann in Zeiten der Unternehmenstransformation relativ einfach sein. Aber wenn wir beginnen, große Organisationen zu verändern, handelt es sich um sehr lange Projekte, die bis zum Kern des Unternehmens reichen und von den Menschen verlangen, auf eine neue Art zu arbeiten und zu denken.“
„Die Umsetzung des Denkens in digitalen Lebenszyklen geht bis in den Kern des Unternehmens hinein.“
Menschen und digitale Zwillinge arbeiten Seite an Seite
Derzeit werden digitale Zwillinge vor allem für teure Geräte wie Traktoren verwendet, aber in Zukunft wird ihr Einsatz im Transportwesen, im Energie- und Luftfahrtsektor, im Maschinenbau, in der medizinischen Versorgung und in intelligenten Städten rasch zunehmen. Der globale Markt für digitale Zwillinge wächst laut Allied Market Research zwischen 2022 und 2030 mit einer atemberaubenden jährlichen Wachstumsrate von
fast 40 %.
„In den nächsten zehn Jahren werden digitale Zwillinge dazu beitragen, die Intensität der geistigen und körperlichen Arbeit des Menschen zu verringern und die Sicherheit und Effizienz der Produktion erheblich zu verbessern. Sie werden in allen Bereichen der Produktion und des Lebens eingesetzt werden“, sagt Dr. Lyu.
Wir stehen am Beginn der „Industrie 5.0“, einer neuen Phase der Industrialisierung, die den Menschen wieder in den Mittelpunkt der Prozesse rückt und mit Technologie, KI und Robotern zusammenarbeitet. Digitale Zwillinge können Menschen dabei helfen, die Bedienung von Maschinen zu erlernen und sogar industrielle Prozesse integrativer zu gestalten. Zum Beispiel kann eine Maschine oder ein Prozess unabhängig von den körperlichen Fähigkeiten der Benutzer:innen ferngesteuert werden.
Digitale Zwillinge können auch eine Rolle dabei spielen, die Arbeit in der Industrie attraktiver zu machen, so Laukkanen.
„Bei der Planung neuer Industrieprojekte müssen wir auch an die Menschen denken, die in diesen Projekten arbeiten. Wir brauchen dringend Arbeitskräfte, also müssen wir Umgebungen schaffen, in denen sich die Menschen wohlfühlen und die Möglichkeit haben, ihre Stärken einzusetzen. Genau darum geht es bei der Industrie 5.0“, sagt Laukkanen.
„Digitale Zwillinge können den industriellen Bereich attraktiver machen.“
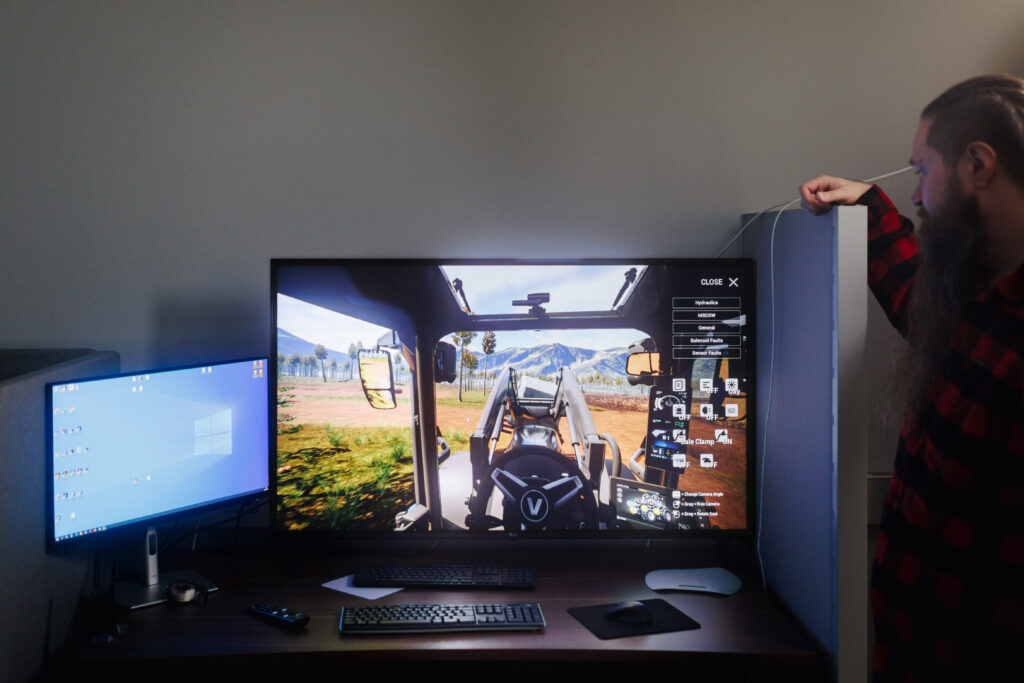
Nächster Schritt: Der digitale Bauernhof
Im Büro von AGCO wurde der digitale Prototyp des Traktors neu gestartet, diesmal mit Asko Kämäräinen am Steuer. Er ist viel besser für die Bedienung der Maschine gerüstet, denn er hat nicht nur zahlreiche Stunden damit verbracht, Simulationen am digitalen Prototyp durchzuführen, sondern hat auch auf dem Bauernhof seiner Familie gearbeitet, bevor er Software-Ingenieur wurde. Damals verfügten die Traktoren allerdings noch nicht über all die ausgeklügelte Software und die mit der Cloud verbundenen Smart-Farming-Lösungen, wie GPS-basierte automatische Lenkung oder Lösungen zur effizienteren Nutzung der Felder.
„Ich wünschte, ich hätte so einen Traktor gehabt, als ich noch auf dem Hof gearbeitet habe. Diese digitalen Funktionen hätten den Unterschied ausgemacht“, sagt Kämäräinen und lächelt.
Der Tag nach dem Interview ist ein großer Tag für den digitalen Prototyp von AGCO: Das Team wird den ersten vollständigen Testzyklus für die aktuelle Softwareversion des kommenden Traktors durchführen, um zu sehen, was funktioniert und um mögliche Fehler zu erkennen.
Olli Kauppinen sagt, dass der digitale Prototyp kein separates Projekt für ein einzelnes Traktormodell ist, sondern ein Werkzeug, um verschiedene Lösungen auszuprobieren und digitale Arbeitsweisen in den gesamten Produktentwicklungsprozess zu integrieren. Vielleicht wird sich in Zukunft ein KI-gesteuerter virtueller Landwirt dem Software-Validierungsteam anschließen und unermüdlich all die verschiedenen Arten simulieren, wie reale Landwirte ihre Maschinen einsetzen, um noch genauere Simulationen zu liefern.
In einiger Zeit werden die neuen Traktoren das Valtra-Werk verlassen. Bis dahin steht der digitale Prototyp für das reale Produkt. Und wenn die Maschinen erst einmal auf echten Bauernhöfen im Einsatz sind, wird der Zwilling wertvolle Daten sammeln, um die Funktionalität zu analysieren und bei der Planung der neuen Traktorengeneration zu helfen.
„Ich glaube, dass die Möglichkeiten, die digitale Zwillinge bieten, ein logischer Schritt in Richtung einer besseren Zukunft sind. Wir haben wahrscheinlich noch nicht einmal angefangen, darüber nachzudenken, was wir erreichen können“, sagt Kauppinen.
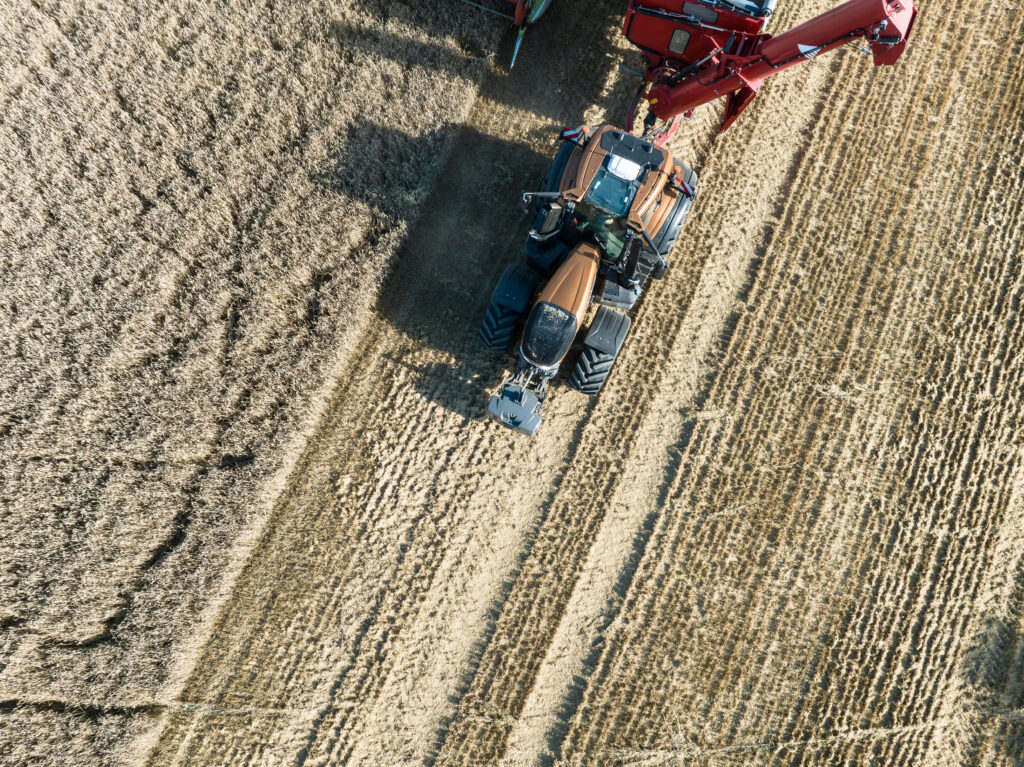