Digital twins are more than a buzzword for industrial companies. Virtual models of physical objects can improve efficiency and cut costs in all stages of product development and product lifecycle. Digital twins and prototypes can transform the way businesses operate – maybe even entire industries.
Expect to learn
- What digital twins and digital prototypes are and how they are used in industrial companies.
- What benefits industrial companies can yield from bringing the physical world into the digital realm.
- How companies can unlock new business opportunities with industry 5.0.
The task is simple: drive the tractor across the yard and pick up a bale of hay. With a turn of the key, the engine starts, and soon the tractor is rolling towards the bales.
The test driver tries to operate the fork, but while they focus on finding the right button on the controls, they accidentally turn the steering wheel. The tractor turns left, straight into a ditch. There it stays, engine still running, the fork sticking to the ground and lifting the cockpit up. The farmyard chickens mill about, oblivious to the accident.
Olli Kauppinen follows the antics of the inexperienced test driver with an amused look on his face. Had the machine been real, an upcoming new version of Valtra tractor worth hundreds of thousands of euros, his reaction could have been very different.
The farm, with its hay bales, chickens, and perilous ditches, exists only in the digital realm.
The test driver is sitting in a tractor seat with real pedals and controls at AGCO’s office in Jyväskylä, Central Finland. We are some 45 kilometres from the factory where the state-of-the-art tractor will be built. Next to the seat are three enormous servers, one of them running the simulation.
Software validation engineer Olli Kauppinen and his team have spent almost two years building the digital prototype of the tractor, the team growing from two to nearly ten people in the process. The digital prototype enables the team to test the tractor’s software without a physical prototype.
The farm, with its hay bales, chickens, and perilous ditches, exists only in the digital realm.
The prototype includes most of the machine’s features – from hydraulics and pneumatics to the engine; the gearbox, and controls. It also imitates the many ways the tractor interacts with the world, like how the shape of the terrain impacts the systems, or the weight of the load.
“We can test the current software and try different kinds of solutions, like new types of sensors, in an agile way. In addition, it’s easier to simulate various errors, such as sensor malfunction, in a digital rather than a physical environment. This saves time in product development,” Kauppinen explains, visibly proud of his team’s accomplishment.
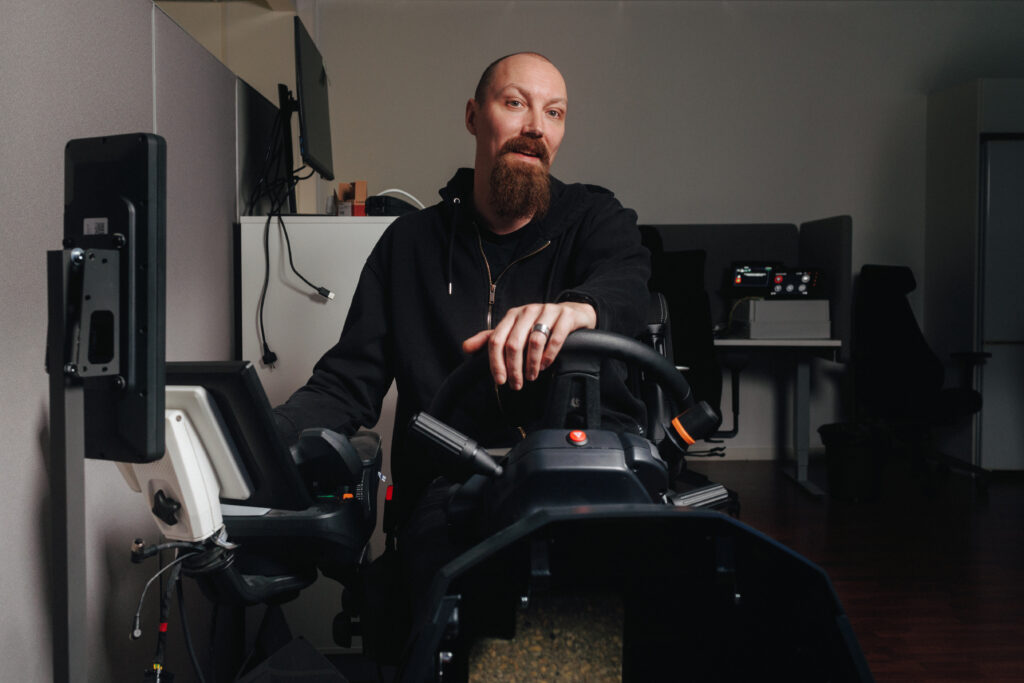
The rise and reign of the digital twin
Digital twins are, in short, virtual models of physical objects. They can be built of a single system, a complete product, or an entire process, like a field or a factory. Some digital twins have a visual representation, like the new version of Valtra tractor on the screen at AGCO’s office, but often they are just data. When there is a real physical counterpart of the product, the virtual model is called a digital twin. A digital prototype, in the contrary, can also be just a virtual version.
The concept holds particular appeal in the manufacturing industry, where the global market for digital twins will reach more than 6 billion dollars (5.5 billion euros) by the mid-2020s, over ten times more than at the beginning of the decade, according to Statista, the German data portal.
The allure of the digital twin is easy to understand; running a digital version of a complex physical object can save valuable resources in the development, production, and testing stages, allowing one to spot possible mechanical or coding issues even before a physical version of the device exists.
Running a digital version of a complex physical object can save valuable resources in the development, production, and testing.
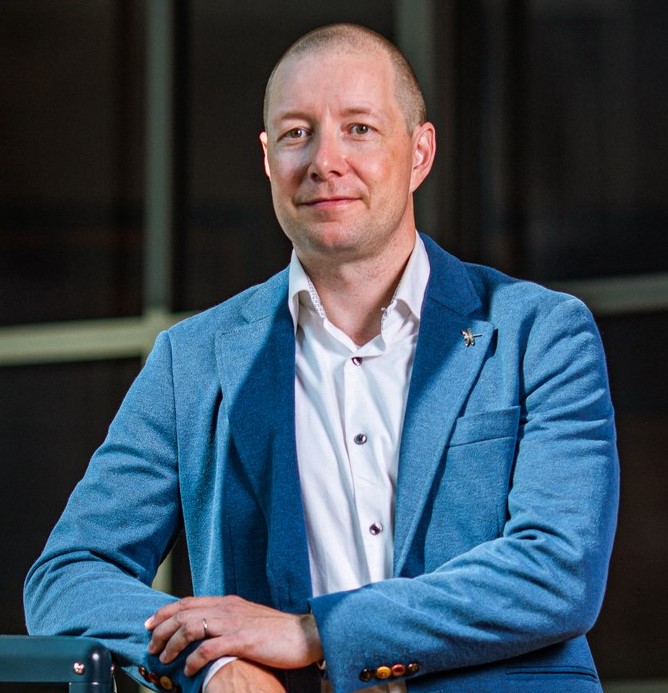
In industrial product development and testing, one of the biggest perks of the digital prototype or a digital twin is that it brings several disciplines under one digital roof, improving and speeding up the development process, says Harri Laukkanen, Director of Industrial Digitalisation at Gofore, a long-time partner of AGCO.
He has a long history with intelligent industry, heavy equipment software and has witnessed first-hand the pitfalls of organisational silos, and how slow and rigid the traditional product development can be.
“In the past, if the machine didn’t work, it meant there was a flaw in the mechanics, the hydraulics chart, or coding. Figuring out exactly where the problem was would take time. Doing this in a virtual environment means we can model and test things like hydraulics and mechanics together with a cross-functional team. This way, we can spot problems right away.”
A digital twin can also be used in training. Learning to operate sophisticated equipment becomes easier, intuitive, and safe – and relatively cheap, as expensive machines end up in the ditch only in virtual reality. The twin is also valuable in spotting maintenance needs and overviewing production, whether on the factory floor or in the field.
Laukkanen believes digital twins can help solve many issues that industrial companies face today, such as rising costs and the pressure to enter the market quickly (but with adequate quality). One of the biggest promises of digital twins lies in assisting companies to navigate an increasingly complex environment where customers and legislators place ever-higher demands on usability, energy efficiency, and sustainability.
“Products, including heavy machinery, are becoming increasingly electric and automated, and we will see more hybrid solutions and autonomous fleets of machines that work together without operators.”
Digital twins can help companies navigate an increasingly complex environment where customers and legislators place ever-higher demands on usability, energy efficiency, and sustainability.
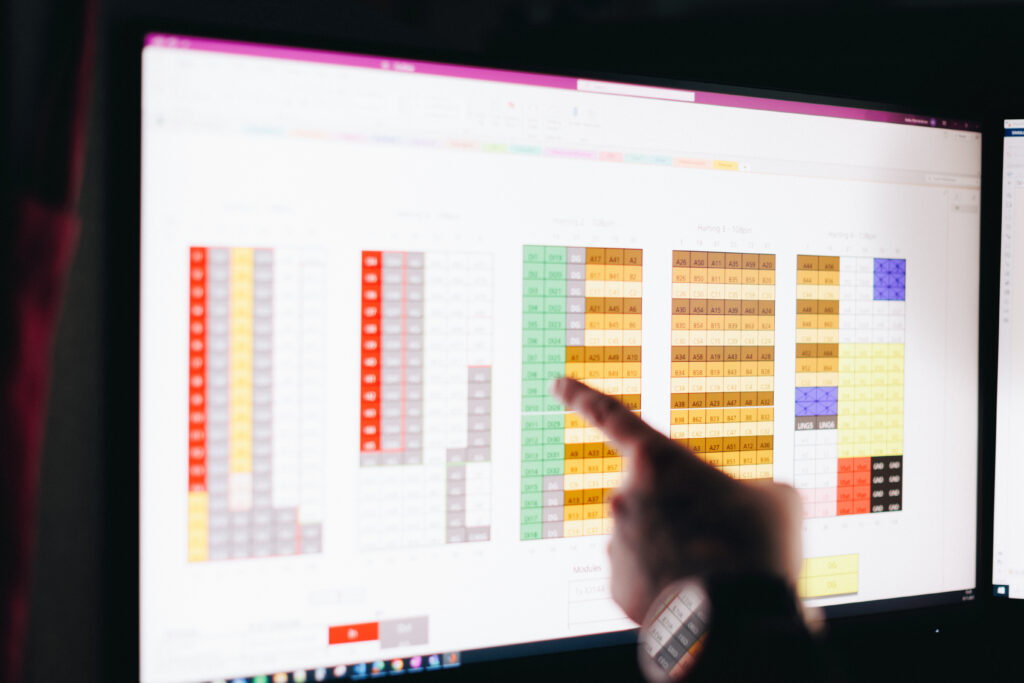
Unlocking new opportunities with the digital life cycle
Digital twins and technologies related to them, such as Artificial Intelligence, the Internet of Things, cloud computing, and the metaverse, are already more than buzzwords in the industrial landscape. Companies worldwide are investing heavily in intelligent products and services, connecting the digital and physical worlds.
According to a report by Capgemini, 88% of organisations will be offering intelligent services in the next five years, and almost half expect that a significant part of their revenue will come from intelligent services.
Taking the physical world to the digital realm opens up immense possibilities for companies. When digital twins are embedded in their strategic planning, businesses can optimise their productivity and operations while also delivering new kinds of experiences, says Dr. Zhihan Lyu, Associate Professor at Uppsala University, Sweden.
“By digitising the constructed world through digital twins, enterprises can unlock the value of their assets for every space in the world, bringing about the emergence of a potentially unlimited number of metaverse services.”
Digital twins are the building blocks of the metaverse, a shared and immersive virtual experience. In the metaverse, companies could, for example, hold remote training and maintenance workshops or view their production facilities. According to McKinsey, the “enterprise metaverse” could ultimately be a fully digital version of the company’s end-to-end supply chain, from raw materials to sales and maintenance.
Companies must do more than add a digital layer on top of the physical world to make the most of digital twins or any other intelligent solution. Gofore’s Laukkanen encourages businesses to consider the entire digital life cycle of a new product, integrating digitalisation all the way into the business model.
“Companies must do more than add a digital layer on top of the physical world to make the most of digital twins or any other intelligent solution.”
“Already at the beginning of product development, we can think of design, and how the machine will be used, or how to fulfil demands of efficiency and sustainability. Thus, we can simulate early on if it’s possible to create a machine with the building blocks we want to use.”
As products become more complex and almost every machine has a digital, cloud-connected heart, configuration control becomes central. Heavy machines, such as tractors, are usually tailored to each customer’s specifications. Digital prototypes can help test all variations well before the machines are built.
Reaching the point where the digital product lifecycle thinking is an integral part of the organisation’s daily operations requires time, strategic planning, and change management, Laukkanen notes. As an industrial digitalisation partner, Gofore helps companies navigate the transformation.
“Implementing digital life cycle thinking into product development and processes can be relatively simple during times of company transformation. But when we start to change large organisations, these are very long projects that go all the way down to the core of the business, and require people to work and think in a new way.”
Implementing digital life cycle thinking goes all the way down to the core of the business.
Humans and digital twins working side by side
Currently, digital twins are used primarily for expensive equipment, like tractors, but in the future, their use in transportation, energy and aerospace sectors, machinery, medical care, and smart cities will rise rapidly. The global market for digital twins is growing at a staggering annual growth rate of nearly 40% between 2022 and 2030, according to Allied Market Research.
“In the next ten years, the role of the digital twins will be to greatly reduce the intensity of mental and physical human labour and significantly improve production safety and efficiency. They will be used in all aspects of production and life,” says Dr. Lyu.
We are entering ‘Industry 5.0’, a new stage of industrialisation that puts people back at the centre of the processes, working alongside technology, AI, and robots. Digital twins can help people learn to operate machines and even make industrial processes more inclusive. For example, a machine or process can be operated remotely regardless of user’s physical abilities.
Digital twins can also have a role in making industrial work more appealing, Laukkanen notes.
“When planning new industrial projects, we must think about the people who work in these projects. The need for workforce is dire, so we must create environments where people can feel good and get a chance to put their strengths to use. That’s what industry 5.0 is all about,” Laukkanen says.
Digital twins can make the industrial field more appealing.
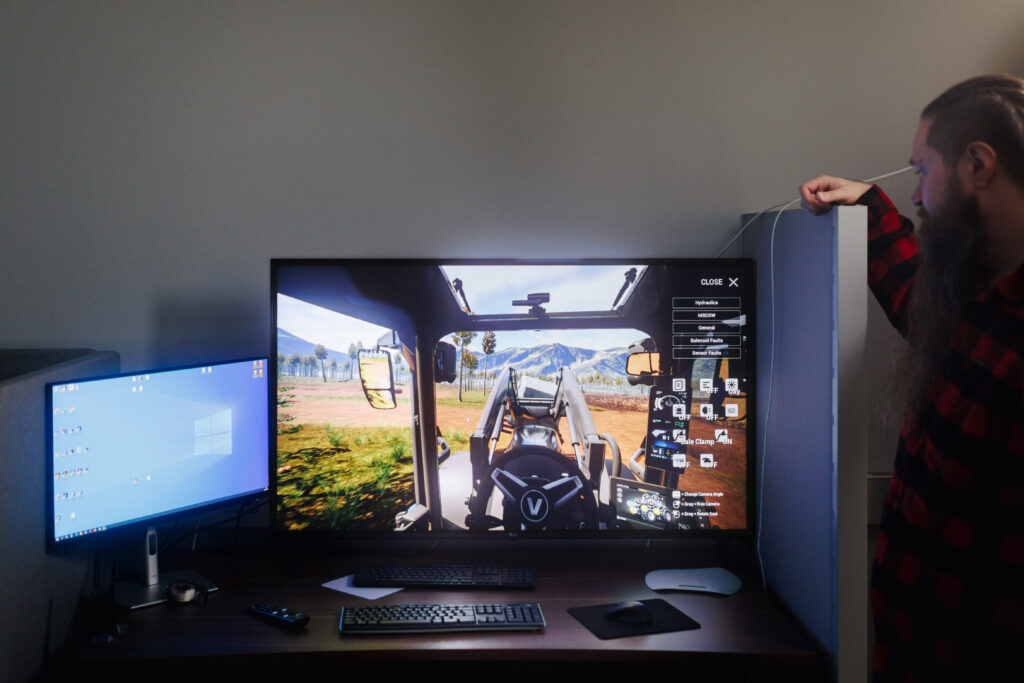
From field tests to fields and beyond
At AGCO’s office, the digital prototype of the tractor has been rebooted, this time with software validation engineer Asko Kämäräinen at the wheel. He’s much better equipped to operate the machine; not only has he spent numerous hours running simulations on the digital prototype, but he also used to work at his family’s farm before becoming a software engineer. Back then, though, tractors didn’t have all the sophisticated software and cloud-connected smart farming solutions, like GPS-based automatic steering or solutions to utilise the fields more efficiently.
“I wish I had a tractor like this when I was still working at the farm. Having these digital features would have made all the difference,” Kämäräinen says, smiling.
The day after the interview is a big day for AGCO’s digital prototype: the team will run the first complete test cycle for the current software version of the upcoming tractor to see what works and to spot potential bugs.
Olli Kauppinen says that the digital prototype is not a separate project for a single tractor model but a tool to try out different solutions and integrate digital ways of working into the entire product development process. Perhaps in the future, an AI-powered virtual farmer will join the software validation team and simulate tirelessly all the different ways real-life farmers use their machines, providing even more accurate simulations.
In some time, the new tractors will roll out from Valtra’s factory. Until then, the digital prototype stands in for the physical thing. And once the machines are toiling on real-life farms, the twin will do a valuable job in collecting data to analyse functionality and help plan the new generation of tractors.
“I feel that the opportunities digital twins offer are a logical step towards a better future. We probably haven’t even started to think about what we can achieve,” says Kauppinen.
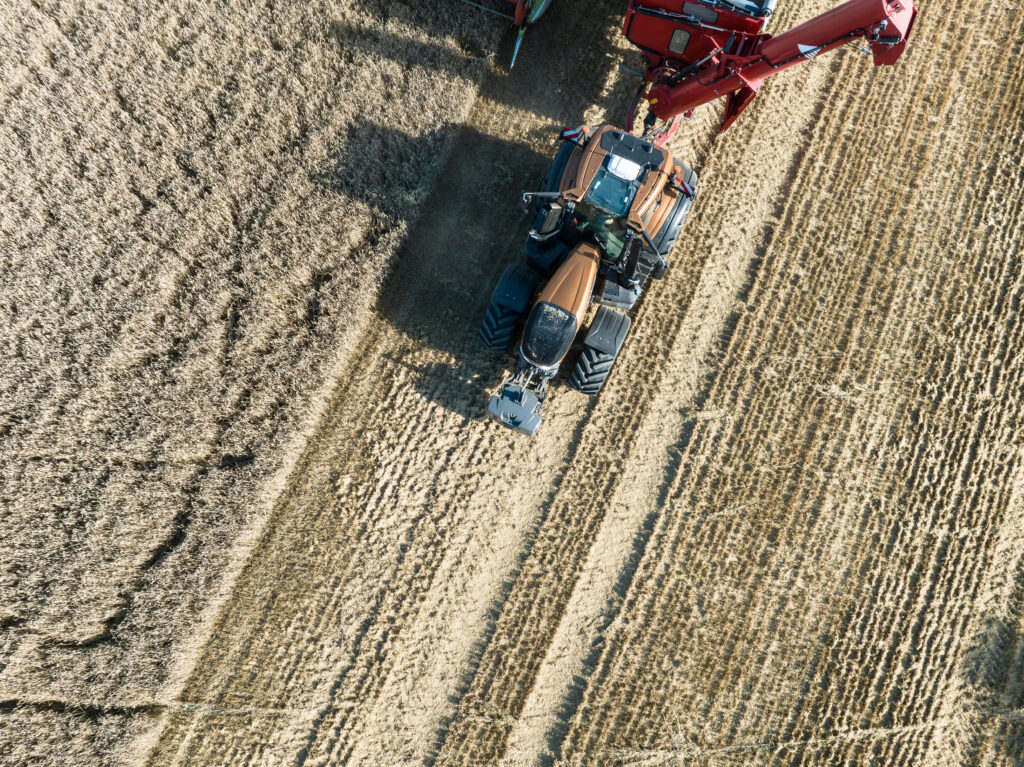