Every technological revolution has forced companies to rethink how work is done. The fifth industrial revolution, or Industry 5.0, puts people back at the core of business. At Neste, digitalisation is primarily a tool for making the 5,000-plus employees even better at what they do.
Expect to learn:
- What human-centricity in Industry 5.0 is all about.
- What kind of capabilities industrial companies and their employees need in digital transformation.
- How humans and artificial intelligence can work together.
Turning on the steam engine on the factory floor in the 18th century meant that industrial labour was no longer limited to human strength and speed. The first Industrial Revolution and every technological revolution since have forced companies and employees to rethink how work is done.
In 2024, companies are again rethinking work with the move to Industry 5.0, driven by rapid technological advances like Artificial Intelligence.
“The fundamentals of work are changing, especially in industrial companies,” says Juho Korpela, Head of AI at Neste, a Finland-based company that refines waste, residues, and other raw materials into renewable fuels.
The latest revolution stands for more than implementing even smarter technology or gaining efficiencies through further automation. What sets Industry 5.0 apart from its predecessors is its human-centricity.
“Digitalisation is all about changing people’s behaviour, not just getting rid of boring routine tasks. Naturally, technology is a big part of it, but value is created through people working in a new way,” Korpela says.
“Understanding this is the key to digital transformation.”
“Digitalisation is all about changing people’s behaviour, not just getting rid of boring routine tasks.”
Dividing tasks between people and technology
Each revolution, whether a steam engine, assembly line, computer, or constellation of data-gathering sensors, has meant reallocating tasks between machines and humans.
Historically, people’s ways of working have been modified to increase efficiency. In Industry 5.0, however, the changes rise from human needs and employee experience: how people use data and machines and how solutions are tailored to serve different user groups.
“We are now redesigning how work is divided between humans and technology,” says Sami Vihavainen, Principal Designer at Gofore.
“This involves examining the processes closely and evaluating which adjustments in task allocation would be most beneficial for human-automation collaboration. It’s crucial to consider where AI is the optimal, if not the sole, choice, as well as areas where it may have limitations.”
While AI often excels in terms of speed, efficiency, and accuracy, it is important to understand the diverse effects of increased automation on human experience. For example, this impact can be observed in cognitive workload, situation awareness, skill degradation, control, and trust.
Industrial companies are investing heavily in automation: automated systems can account for up to 25 per cent of many companies’ capital spending over 2022–2027, according to McKinsey Global Industrial Robotics Survey.
However, full automation shouldn’t be the sole goal of digital transformation. Vihavainen encourages companies to focus on humans and technology working side by side.
“Do we see people as something that can be replaced, or do we see them as collaborators with technology, who perhaps need more education to use it?”
At Neste, digitalisation is primarily a tool for making the 5,000-plus employees even better at what they do, says Korpela. Preventive maintenance in refineries offers an excellent example of how digitalisation changes both human behaviour and the content of work.
“We monitor each facility at all times and try to prevent big and expensive issues, such as long maintenance breaks, with smaller fixes and smaller maintenance activities. Doing preventive, data-based maintenance instead of following a pre-planned maintenance calendar changes the way work is planned and how it’s done. Here, digitalisation doesn’t remove the human’s work but changes what is done and how.”
“Do we see people as something that can be replaced, or as collaborators with technology?”
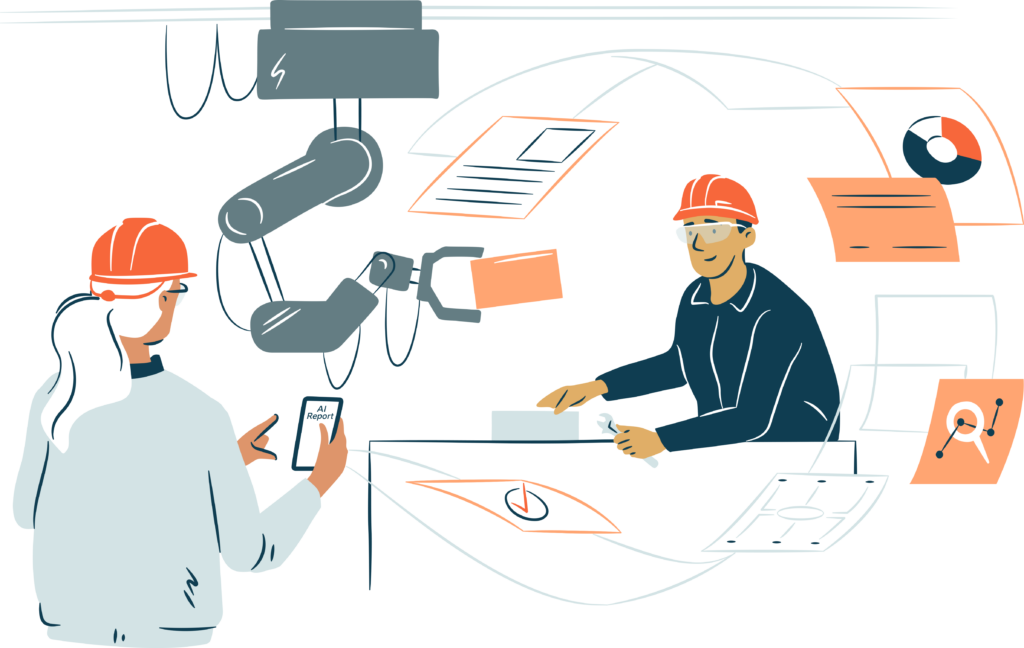
Pairing employees with AI
If the star player of the first Industrial Revolution was the remarkably powerful and cost-efficient Watt steam engine, in the fifth it’s Artificial Intelligence. Manufacturing is much more likely to benefit from the adoption of AI than many other sectors, as the industry creates significantly more data than fields like communications, finance, or retail, according to Deloitte.
Putting the data to use has significant financial benefits. According to a McKinsey report, AI can deliver 1 trillion dollars’ worth of additional economic activity in the industrial sector. Applying AI has led to a 10 to 15 per cent increase in production in some processing plants.
However, industrial companies shouldn’t be too fixed on increasing operative efficiency when looking into adopting AI, Vihavainen says. They should also explore what opportunities could be unlocked by pairing AI with humans, whether it’s a new way of working or a completely new service.
Generative AI, or systems capable of producing new content based on massive amounts of data, is also making its way into industrial operations. The goal is to enable robots to better understand the world and its unpredictable situations – and allow humans to interact with machines using natural language. For example, an employee could simply change the robot’s task by typing in a new command in their native tongue.
Involving employees in implementing AI is crucial to the project’s success. Vihavainen talks of a recent change management project led by Gofore, where the employees were actively involved in figuring out how AI would be used in their work.
A significant part of the process was planning how AI would impact the ways humans interact with each other. AI can produce new kinds of scenarios or suggest unprecedented improvements, which people then need to discuss and evaluate together.
“In essence, we were designing the organisation and the AI solution simultaneously, involving all parties as much as possible.”
At Neste, AI is part of almost all business areas, from the refinery process to pricing, logistics, and marketing. The company uses machine learning to make future projections, and AI is part of many everyday processes, like planning and reporting. AI’s primary role is creating new data sets for people who can use the data to do their job better, Korpela explains.
He points out that the value of digitalisation is often indirect and is realized through improved processes. When logistics planners have the right tools and data at their disposal, they can for example optimize vessel speed, which in turn leads to shorter waiting times in ports, smaller fuel consumption, and lower CO2 emissions.
“If our people can do their jobs better and are more satisfied with it, and at the same time we manage to lower costs and emissions, there must be a correlation. It always starts with the people: they are the ones we build tools, data sets and AI models for, and it’s them, not the AI, who bring home the value.”
“It’s people, not the AI, who bring home the value.”
Less jobs or more meaningful jobs?
Each industrial revolution has sparked a fear of job loss in its time. In the early 1800s, English textile workers even destroyed machinery because they were afraid for the future of jobs.
The latest revolution has also raised concern. According to a 2023 report from the OECD, 57 per cent of manufacturing employees are worried about job loss due to AI in the next ten years.
If people are not at the heart of it, new technology can erode working conditions and reduce job satisfaction, writes Anna Thomas, the co-founder of the Institute for the Future of Work, in The Guardian. Therefore, companies must invest in human capabilities: “Investment in this context is not about the amount spent on software or training to use a system, it’s about an orientation towards human agency, about people feeling they are being invested in.”
Companies must focus on careful change management to alleviate worries and increase understanding of opportunities, says Jaana Vuori, Principal Consultant at Gofore.
“Once people have understood why something is important for the company, we need to bring the topic into the teams and personal conversations so that people truly understand what the new technologies mean to different roles.”
Vuori says an employee showing involvement in change is a strong indicator of a transformation project’s success. Thus, it’s important to follow not just money or other hard metrics but also the sentiment within the organization. Getting people involved and willing to adjust their ways as well as providing enough training and education for them is vital.
“Change is never created from fear. We need to get people into an excited mindset.”
It’s important to follow not just money or other hard metrics but also the sentiment.
Human-centricity can also be an asset in competing for skilled workers. This involves enhancing collaboration between humans and technology, ensuring inclusivity of systems and work methods, and considering the needs of people with disabilities or neurodivergent employees.
“The new generations entering the workforce expect a new kind of meaningfulness from work.”
Vuori believes we have arrived at a turning point. The previous industrial revolutions have focused almost solely on the advances of technology, but now it’s time to discuss the effects technology has on us and the world.
“Previously, we have been quite enchanted by the technology. Now people want to stop and think about how it impacts us and the environment.”