The amount of software in devices and equipment has grown significantly in the last decade. Features implemented through software enable personalisation of equipment to the customer’s individual needs and the addition of features that are difficult or impossible to achieve otherwise. The increasing number of software features, however, comes with its own set of challenges for production.
To put it simply, one factor almost always affects several others in devices consisting of both mechanical features and software. Take, for example, a passenger car. An electronic handbrake is chosen for the model. This one feature immediately affects ten parameters that need to be put together in production, and if there are several features like this, there will be even more parameters to link.
Managing these combinations is at the moment, largely manual work – it is slow, prone to mistakes, and takes up many work hours; and as the number of combinations, so has the work needed to manage them.
Crouching risk, hidden problem
When smart features were added to mechanical devices earlier, there was only a modest amount of software, to begin with, and the number of parameters linked to them was feasible for them to be managed at the production stage.
But as the amount of software in use has grown, the number of combinations needed to be done manually has exponentially grown.
Parameter management might, for now, have remained under control, but in many manufacturing industry companies, it has reached a critical point. The situation might not have yet spun fully out of control, but it’s getting risky. So far, the only thing stopping the situation from hurtling out of control are the skills and experience of the people in charge of production.
What does the problem consist of?
Device production has changed as software use has increased. Where earlier the device itself and its mechanical features took centre stage, and then the software features would be added on to differentiate the product, now software is an integral part of any complicated machine.
Again, a passenger car is a good example of this. Before, the car might have been chosen primarily for its mechanical features, and software brought luxury gimmicks to the vehicle; but now most of the features a buyer chooses are either completely software-integrated or software-assisted at the very least.
The amount of software just keeps on increasing and in terms of production, this means a monumental amount of new parameters and combinations to put into place.
An illustrative metaphor might be making gingerbread. The software variants and parameters are the dough that you’re going to make into biscuits with your production. But before you can put them in the oven you need to cut them into the right shape. If the parameters are put into place manually, it is as if you are trying to make the biscuit shapes without a cutter.
This manual work is slow and prone to mistakes, and directly affects the quality of production. With larger orders, it can also result in scalability problems.
Configuration management is the solution
In order to automate the parameter combinations, connections need to be created between the systems involved. These can include for example
- Product information management
- Order management
- Production management
At the moment, the work is more or less divided between these systems so that in the product information management system you find all the software and parameter variations; in the order management you find the features that the customer has chosen to have in the device; while the production management combines these into their final form.
The processes between these systems can be run with configuration management, which is an important part of the wider concept of product lifecycle management (PLM). Configuration management is in effect the gingerbread cutter (referring back to the gingerbread analogy earlier).
With configuration management, the desired features for the device can be retrieved from order management, and the parameters linked to those features can be retrieved from product information management, at which point they can be sent to production in the form of work orders.
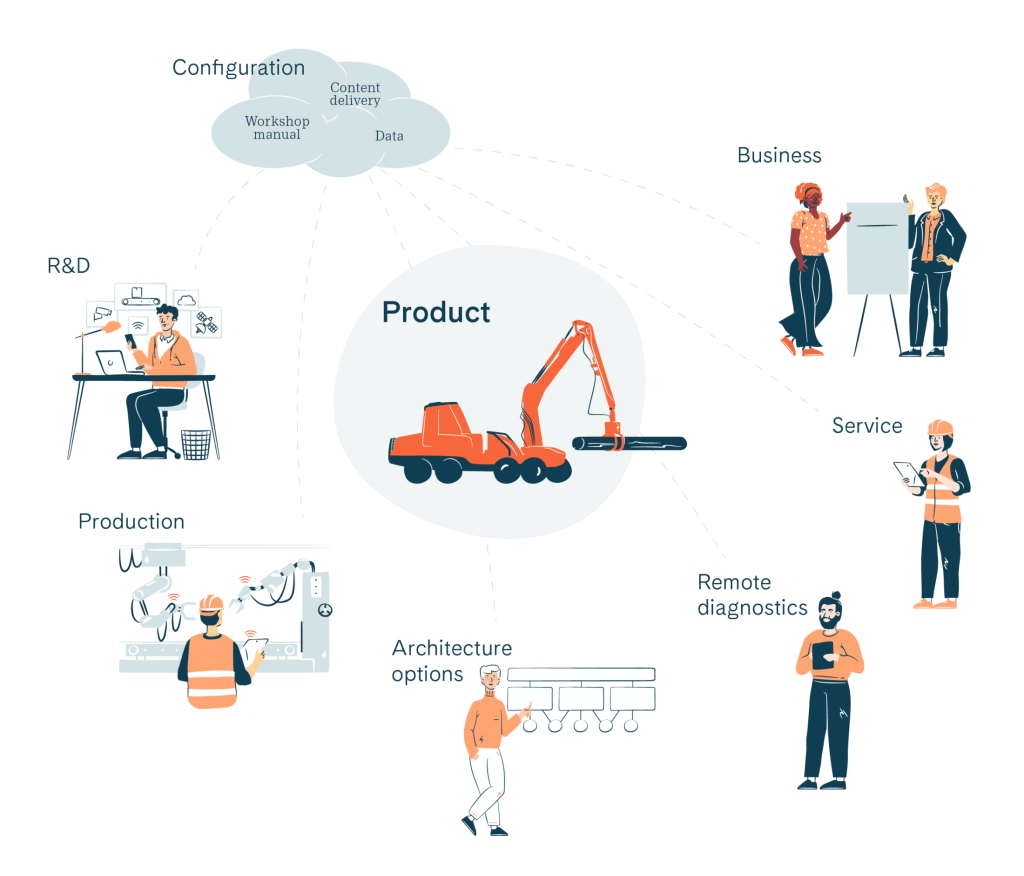
What’s the point of configuration and PLM?
When the amount of manual work needed is less, it frees up more time for production management to ensure that quality steadily improves, and the skills of those who were previously managing structures of production can be directed to developing production; thus making it easier for production to grow.
Another significant benefit is that the devices produced are traceable. When parameters are connected by hand, there is rarely any clear documentation of this. With automation, each device comes with an electronic “birth certificate” to which any software updates are added later, so it can be used for troubleshooting, guarantee issues, and post-marketing.
Thirdly, the system generates a digital or virtual copy of the physical device produced. The copy can also be created before actual production, and this then opens up all new kinds of possibilities for thoroughly testing the device before manufacture.
Nothing new under the sun?
At the end of the day, we all sometimes feel that we’ve heard it all before. Things have been done a certain way just because they always have been done that way, and for good reason. Then circumstances change, and the way things are done no longer seems to work. These are the kinds of situations that force businesses to have to change their ways.
The silver lining in this hidden problem is, that it also opens up new business opportunities. Every manufacturing company has to take some kind of a stance in this regard, and while you are thinking about what yours will be, think about how you will turn this challenge into an opportunity too.
A digitalised product life cycle enables less costly RnD and production, predictable maintenance, and more sustainable functions.